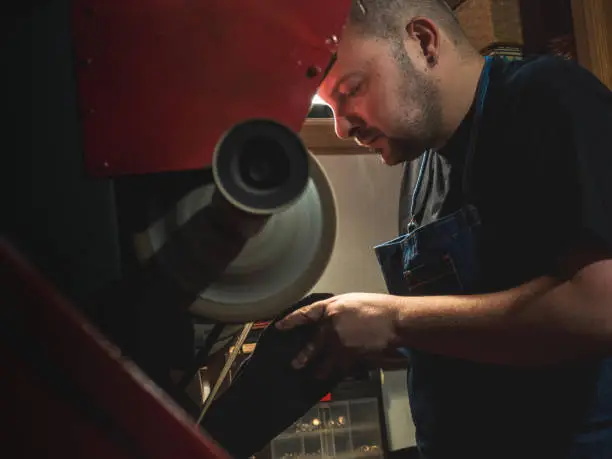
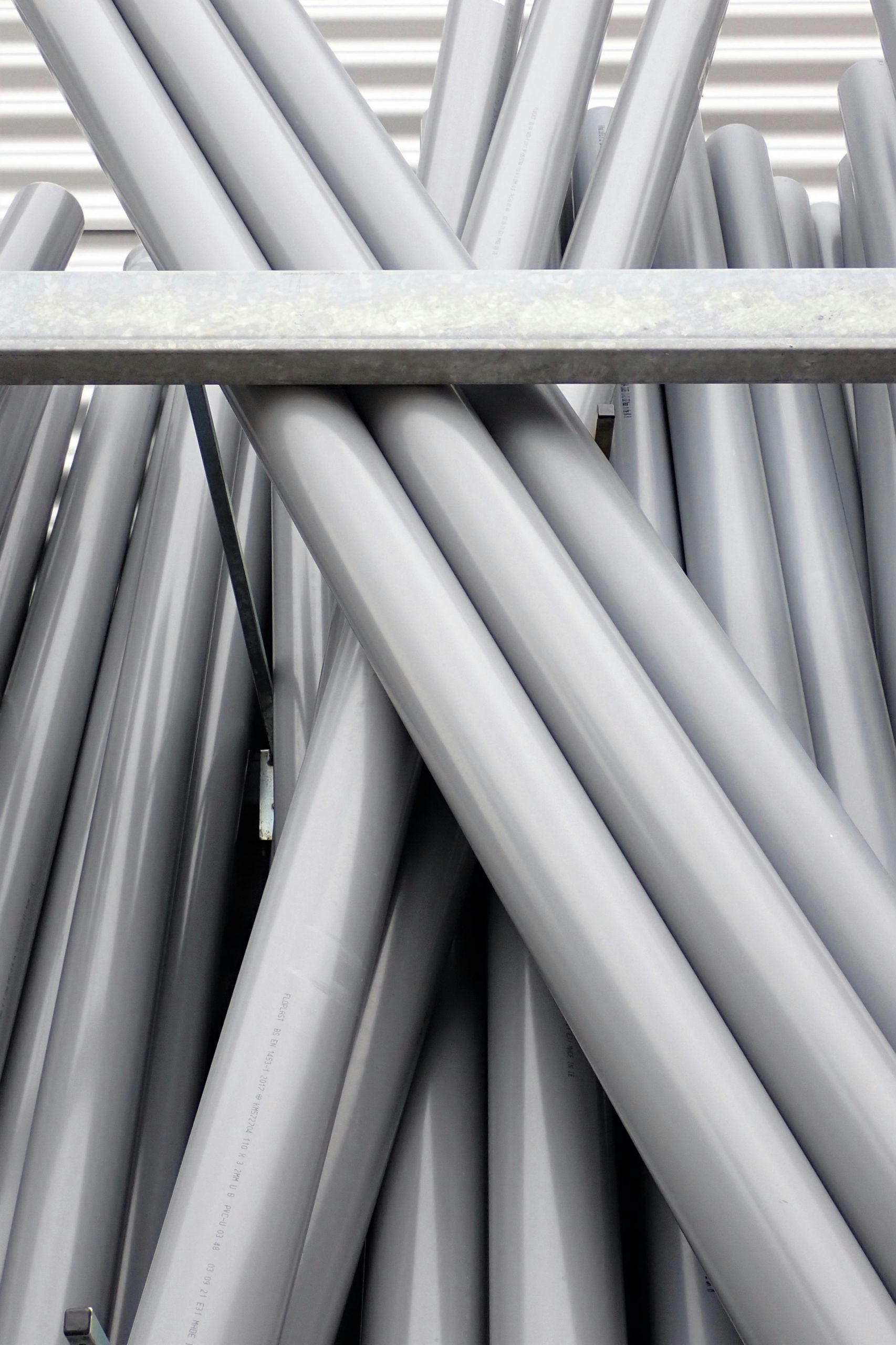
What is metal swaging?
If you’ve pursued options for cold forming metal parts before, you’ve likely come across the term ‘swaging’. Even with a surface level knowledge of engineering and manufacturing, this process might be a mystery to many. This article is designed to provide essential knowledge around metal swaging, including what’s involved in the process and how it can be used to benefit manufacturers.
Metal swaging explained
Metal swaging, pronounced ‘swedging’, is a technique for cold forming metal to the shape of a pre-made die. The process sees the metal deformed through the application of steady force, with the end shape of the product being influenced by the shape of die. A sheet metal swaging machine can use multiple split dies mounted inside its cage, along with rollers to apply force. One of the main uses of swaging is to reduce the diameter of a workpiece, thereby creating a point that seals the end of a tube. It is this reason that metal swaging is used in the Aerospace and Safety industries, as well as many others where manufacturing is required.
Swaging is just one of many modern metal forming options that businesses have access to. Others include metal spinning, laser cutting, use of a metal press, and machining. Expert metal spinners can control this reduction to meet exact specifications.
The metal swaging process
As a business owner who’s looking to outsource the manufacturing of metal parts, it’s important to get an insight into the processes that are available. This will not only help you decide which is best for your project needs, but also provide an insight into what is possible through a certain approach. The simplified process for metal swaging follows:
- Preparation – Before swaging takes place, it’s important to consider the material being used as this will dictate how much force is necessary to achieve a certain degree of deformation.
- Sie selection – As mentioned earlier, swaging involves using dies to deform the metal, which are tools with shaped holes or profiles. The appropriate die or dies are selected based on the desired shape and dimensions of the final product.
- Insertion – The metal is inserted into the die. This may happen multiple times if it is needed to achieve the desired result.
- Deformation – Pressure is applied to the metal using a swaging machine. This could be through pneumatic, hydraulic, or mechanical means depending on the equipment. Controls on the machine allow for the amount of pressure and the speed at which it is applied to the metal to be adjusted. The result is that the workpiece takes on the shape of the die or dies.
- Quality control – Throughout the swaging process, quality control measures are typically implemented to ensure that the finished product meets the required specifications of dimensions, tolerances, and material properties.
Once the operator is satisfied that the workpiece has achieved the shape and dimensions specified, any metal finishings can be applied to the workpiece.
Solutions for metal spinning projects
Tanfield Metal Spinners have the capabilities to complete large scale projects that require precision cold forming. This includes efficient techniques such as metal swaging. Simply get in touch with us using the ‘Talk to an Expert’ form on our website and a member of our team will be happy to discuss the goals of your project. We are able to provide design drawings alongside quotes for those who don’t have any prepared.